Have you ever wondered how the meat is processed? Automation technology effectively addresses to the global meat industry to increase yield from raw materials and eliminate waste. Automation equipment allow to enhance labour efficiency, reduce staff training requirements, eliminate many physically demanding tasks from the processing chain and improve product quality. One of the main problems is product variability.
Scott company from New Zealand has solved variable lamb carcass problems through mechatronic solutions that adjust the most extreme carcass variations through measuring carcass dimensions with X-ray technology to optimise cutting accuracy, product cut selection, reduced manual handling of carcasses and improved cleaning technology.
Automated X-ray Rib Identification software:
Scott Automated Boning Room System
Scott manufactures both stand-alone machines and fully integrated systems that transfer products from one machine to another.
1. X-Ray system is designed to determine the skeletal structure of a carcass and determine the ideal cut points for separation of the forequarter, middle and hindquarter.
2. The X-ray primal system can produce the primal cuts of a carcass including forequarter, middle, loin and hindquarter at a rate of up to 12 carcases per minute. The system uses an X-ray camera to scan the skeletal structure of the carcass, identify the most profitable cut positions, then cut the carcass to within 2mm of accuracy. The cuts are made with two counter rotating circular blades which create no saw dust. Not only does this eliminate band saw waste but it is considerably more accurate than a band saw operator, so that loin and rack yield is maximised. The X-ray system can also be configured to provide real time measurement of the yield from each primal, making it possible to optimise product management from more than just carcass weight.
3. The forequarter system is made up of a robotic arm which grasps the forequarter, and processes neck chops, knuckle tip, shank, atlas and vertebra split. Cut accuracy is higher than can be achieved with a human band saw operator and it removes the safety hazard involved with band saw operation.
4. The middle system is comprised of several stations that can be configured according to the customer's requirements. The stations conduct the following operations:
- Removing Spinal Cord: The middle is automatically loaded into the machine which locates the spinal cord holes at either end of the saddle section then, with a combination of vacuum and compressed air, removes spinal cord materials to a vessel.
- Splitting Station: This splits the loin from the rack and features a yield maximising scallop cut which can not be performed by a band saw operator. There is no band saw waste.
- Flap Cutting: Flaps are accurately removed to the precise distance specified from the edge of the eye meat. The distance from the eye meat is automatically measured for each saddle.
- Chining: This chine the bones the rack saddle, with cutting blades adjusted according to the size of each individual rack. Automatic adjustment here can add up to 5 grams of yield per carcass.
- Splitting: The rack saddle is split perfectly down the spinal cord hole.
5. The hindquarter system uses a robotic arm to automatically cut the leg from the aitch bone. This system achieves consistently higher yields than it is possible with manual boning.
The following video shows the fully automated bone-in lamb deboning system:
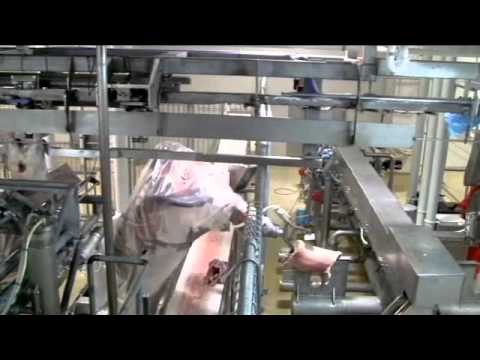
Comments